But what happens when we combine the two?
Industrial flexibility will play an increasingly important role as industry moves towards electrification.
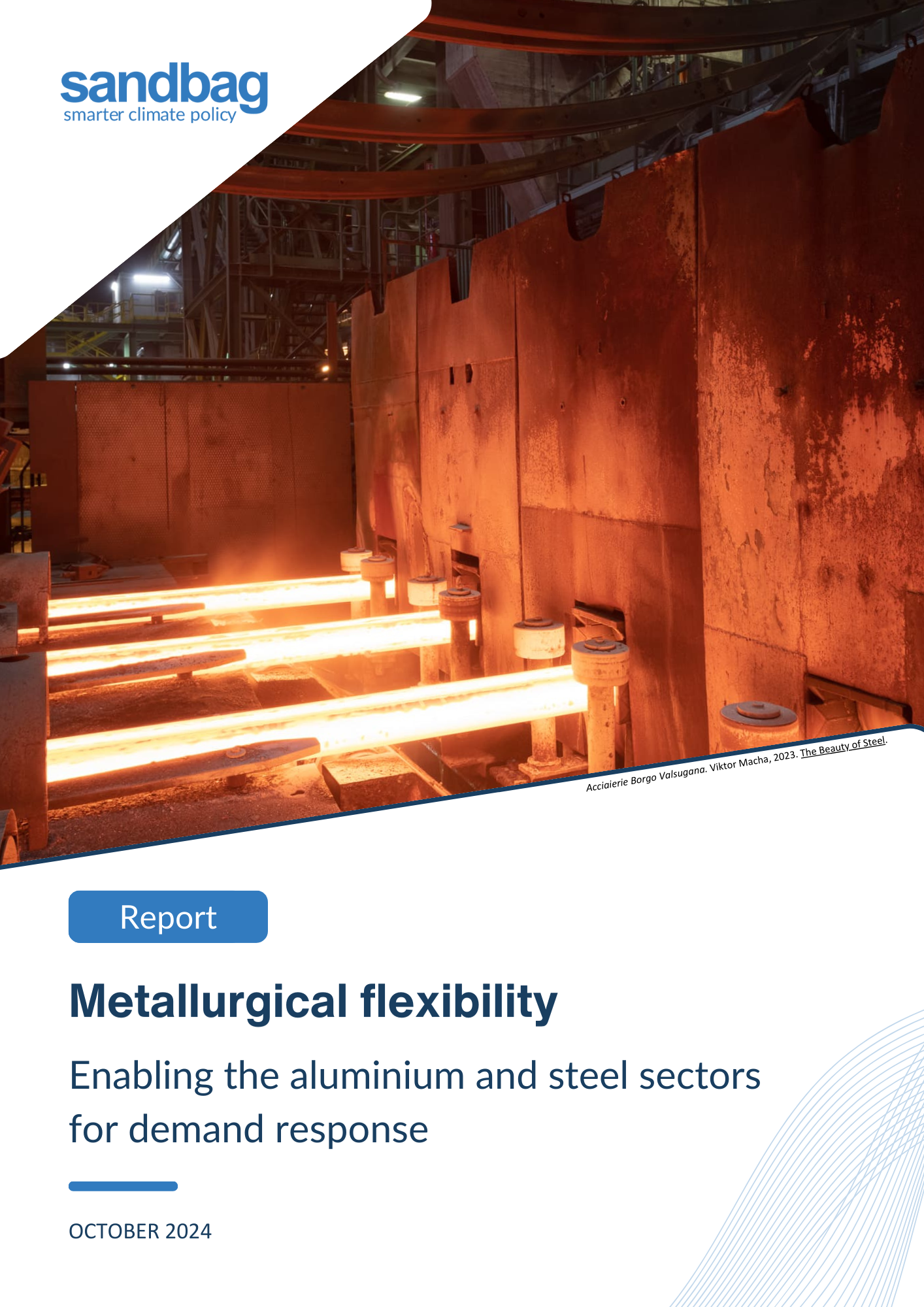
About the report
This report examines demand response as a key strategy for phasing out fossil fuels in electricity systems, especially as we integrate more intermittent renewables. If electricity supply cannot always meet demand, then demand will have to adapt – and large industrial consumers have a big role to play.
Challenges and opportunities of flexibility
Flexibility does not necessarily lead to a loss of production
- In primary aluminium smelting, the strong link between energy input and production, together with the physical constraints of the smelting process, limits the ability of these operators to fully engage in demand response. However, emerging retrofit technologies show promise in enabling these industries to provide regular and intense flexibility to the power grid.
- In contrast, hydrogen-based steelmaking offers immense flexibility potential. Unlike aluminium, where flexibility comes from adjusting energy inputs, steelmakers can balance feedstock between virgin iron and scrap. This allows them to shut down equipment completely and reduce their energy consumption by more than 80% for several hours each day, depending on the proportion of scrap used.
A necessity to adapt for industrial operators
Key takeaways
- To maximise renewables integration and cost-effectively upgrade grids, non-fossil flexibility instruments must replace traditional capacity mechanisms to reduce reliance on thermal power for balancing and ancillary services.
- Building flexibility into industrial processes requires new strategies, from oversizing machinery to storing excess production.
- Due to the wide variation in operating costs, efficiencies and profit margins between plants, fair compensation for demand response requires tailored bilateral negotiations with grid operators, as a one-size-fits-all approach is impractical.
- Industrial flexibility does not necessarily lead to lower production output.
- Investment in additional renewable capacity is critical to avoid overloading the grid and triggering thermal generation.
- Industry participation in demand response is only the first step towards a fully flexible, fossil-free electricity system.
Photo by Tayssir Kadamany from Canva
Related publications
Heat up industry, not the climate!
This position paper analyses the European Commission’s industrial heat auction, highlighting the importance of auction design to ensure electrification reduces emissions without causing unintended increases due to electricity grid dynamics.
Extending the CBAM to indirect emissions
Sandbag’s latest brief outlines why the CBAM must include indirect emissions — and how this would improve climate effectiveness, industrial fairness, and fiscal efficiency.
New Principles for Steel Labelling: response to the consultation on the Industrial Decarbonisation Accelerator Act
Sandbag’s response to the EU’s Industrial Decarbonisation Accelerator Act sets out four principles to guide green steel labelling schemes, promoting credible standards based on lifecycle emissions and system-wide decarbonisation.